Casting Creations
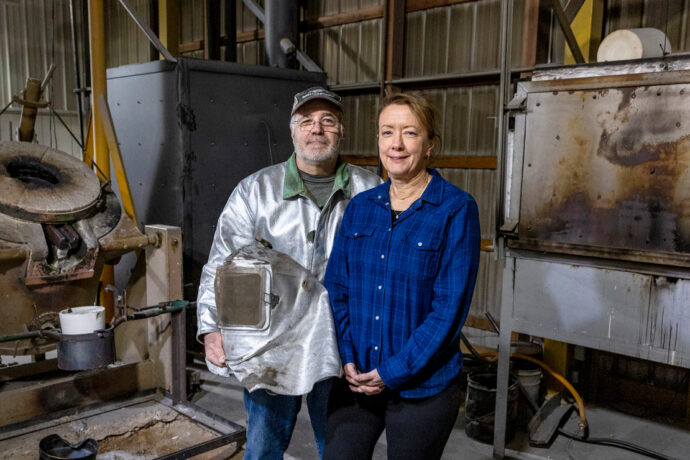
Howard Lake, Minn.
By Maria Surma Manka | Photography by Paul Middlestaedt
You can’t speed up the artistic process, and few people know that better than Wes Jones, owner of Casting Creations of Minnesota. Working with metals at his foundry and fabrication shop, Wes and his team create sculptures of stunning detail and size.
“A mold can be a two-week process. Ceramic takes up to 10 coats and it’s one coat a day. A life-size sculpture is four-to-six weeks minimum,” said Jones. But good things come to those who wait, as Casting Creations’ sculptures will likely last several lifetimes.
Wes and his wife, Lori, co-own the business. Part foundry and part fabrication shop, Casting Creations primarily produces custom art sculptures. “Typically, an artist designs it and we do the casting and molding and finishing,” explained Jones.
Jones, his wife, and four employees create statues, memorials, plaques, and public works of art for individuals and organizations around the world. Every job is different because every job is custom.
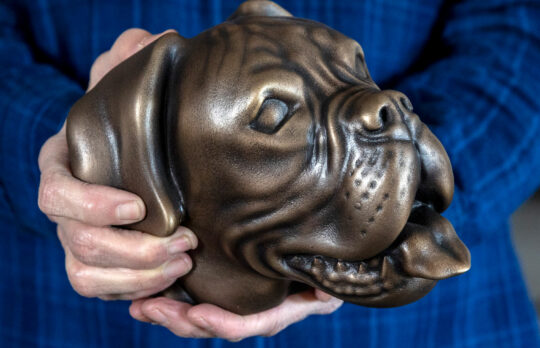
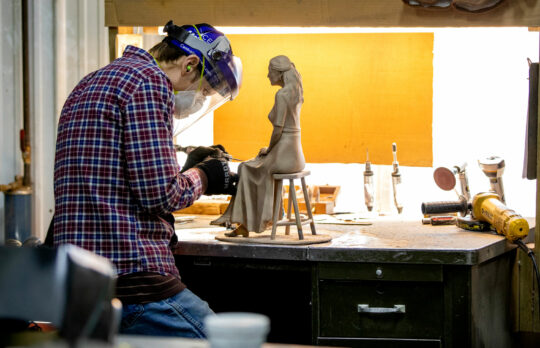
We caught up with Wes to learn how he brings art to life.
- Casting work involves melting metal and pouring it into a mold. Although aluminum casting is an option, most artists choose bronze because of its durability and aesthetic.
- Fabrication projects use bronze, aluminum, steel or stainless steel. The team creates shapes out of metal sheets, plates, tubing and other materials. Unlike casting work, no metal melting is required.
- In recent years, much of Casting Creations’ work comes from zoos, museums, and government. These customers typically request large bronze sculptures due to their beauty and durability outside in the elements.
- To better serve the sight-impaired, museums request extremely detailed animal sculptures that can be handled and touched by visitors. “We’ve made things like frogs, beetles and snakes. They have to be very accurate so people feeling them can get a sense of the animal,” Jones explained.
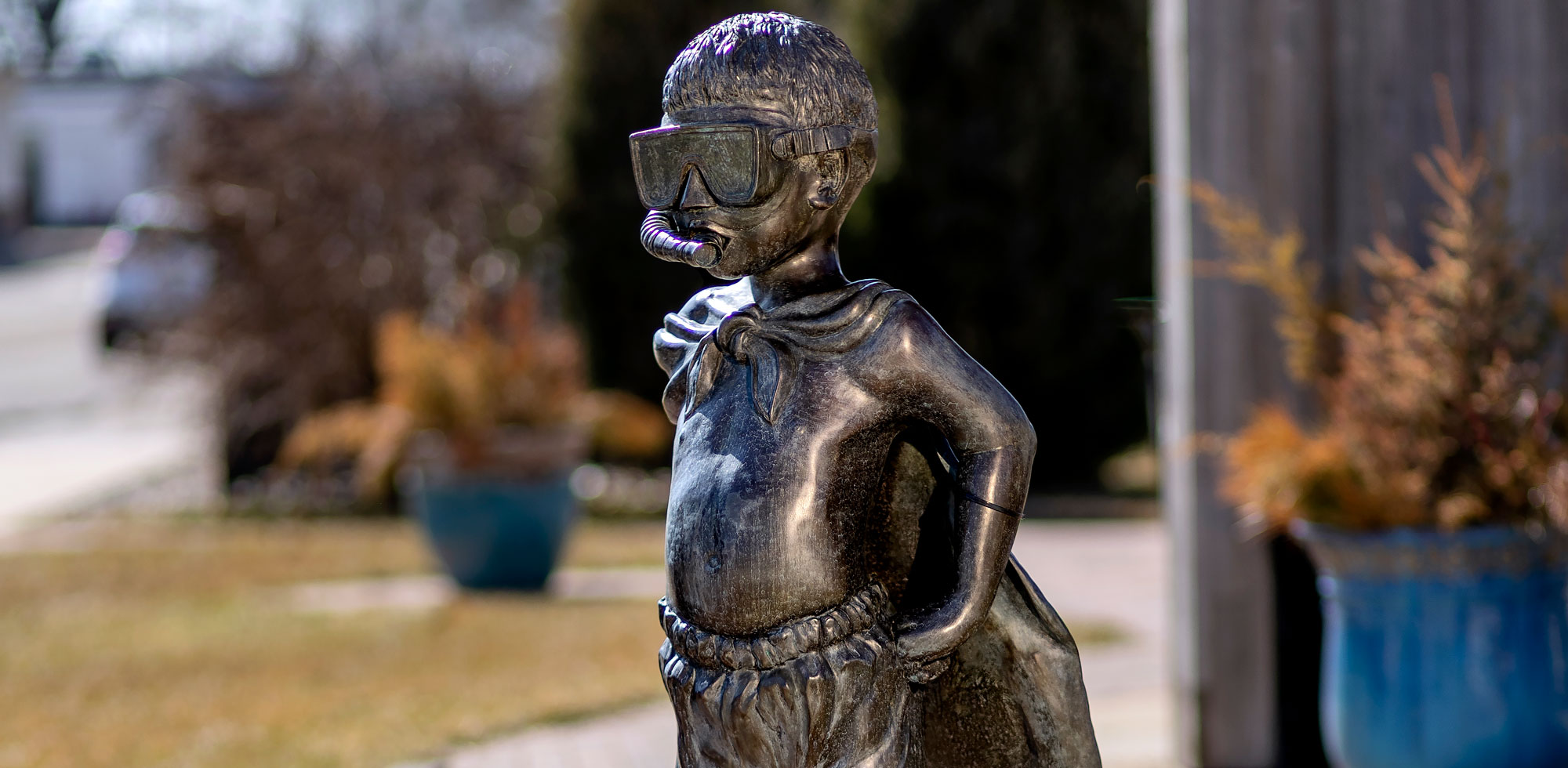
- Casting a sculpture is a complex process and varies by the size and metal ordered. If an artist wants a bust cast, he or she first creates a bust out of clay, wax, or other material.
- Jones and his team then apply a rubber urethane material to the clay surface, covered by rigid plastic. After that sets and hardens, the plastic is split off and the rubber is removed and serves as the casting mold.
- A special wax is then melted and poured inside the mold. The mold is removed and the wax is coated several times with ceramic to build a shell. After a few weeks of applying and drying the ceramic, the wax gets melted away while the ceramic holds its shape. Liquid metal is poured into the area where the wax was melted out. After the metal solidifies, the ceramic is blasted off and the piece goes to finishing.
- For very large pieces, like a hippo or a human, the sculpture is cast in pieces. Legs, arms and torso are separately made and welded together. Small details are applied so the welding seams are virtually invisible, even to Jones’ eye.
- The metal for Casting Creations comes out of Chicago. Bronze is 95 percent copper, and the copper is generated entirely from recycled materials, like scrap wire and metal. The wax is a waste product from the oil industry, that is inexpensively sold to foundaries. Ceramic is specially prepared sand that comes from different places throughout the United States.
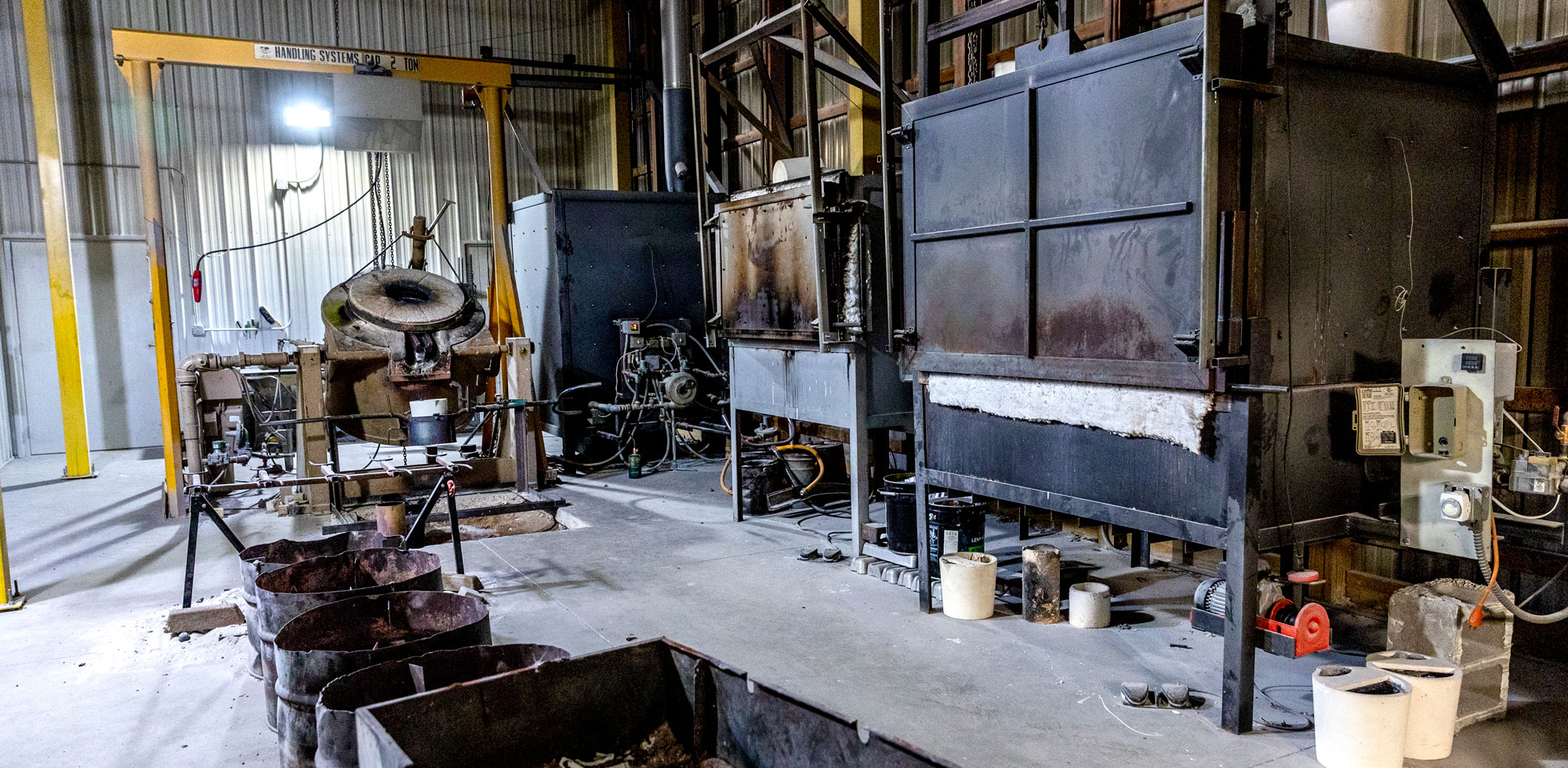
- Although custom projects are the bulk of the work, Casting Creations also makes a line of animal cremation urns. Cast in bronze at 2,200 degrees, the urns are handmade but take less time and custom work, freeing up Jones’ schedule as he considers what sort of retirement he wants.
- Jones relishes the problem-solving and creativity of his work, and some of his employees have decades of experience in their craft. For especially complicated pieces, Jones consults with software engineers, mechanical engineers, structural engineers and robotics engineers.
- Casting Creations received a Minnesota Main Street COVID Relief Grant, administered by the Initiative Foundation. The grant was instrumental in helping the company survive pandemic lockdowns, the rising material prices and the drop in customers. “It was touch-and-go for a while. We had no sales for a month,” said Jones. “It was great to have the extra money to help us get through it.”
Related Articles
Long Prairie Drive-in Theater
This magical Minnesota landmark makes it worth the drive to watch a movie. Read More
Adrienne Benjamin
Benjamin crafts career as Anishinaabe artist, equity advocate, cultural educator. Read More
Redhead Creamery Spirits
Redhead Creamery is diversifying its dairy and entering a new market: distilled spirits. Read More