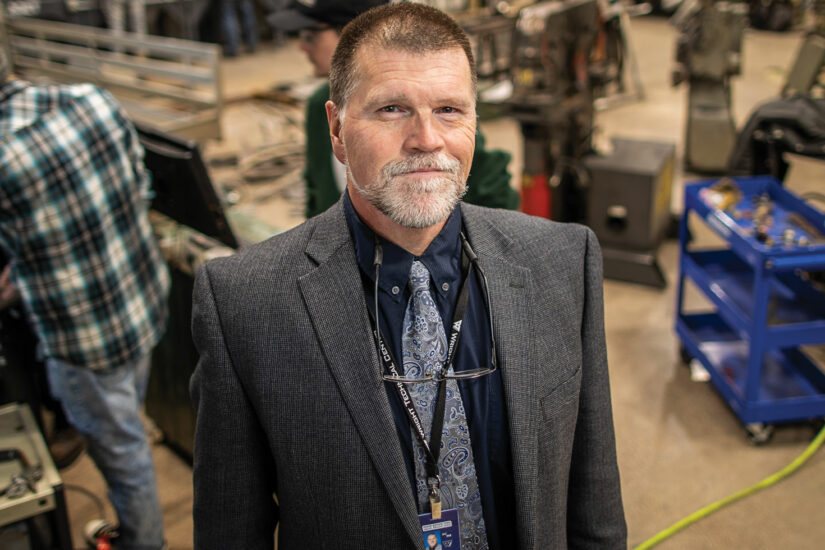
Where Skills are Gold
Wright Technical Center expands training options for students who are eager to find a future in hands-on trades and industrial careers.
By Lisa Meyers McClintick | Photography by John Linn
By mid-afternoon, the hydraulic whir of automotive lifts goes quiet and the smell of fresh sawdust and hot metal fades from the workshops of Wright Technical Center, a cooperative of eight school districts that focuses on hands-on trades and industrial skills. Unlike most high schools, no Nikes squeak across gym floors. And no music comes and goes from the band room.
But it’s the silent hours at this specialized non-traditional high school in Buffalo that some area leaders see as an opportunity. That’s because Wright Technical Center opens its doors to adults, too—a solution that also benefits Central Minnesota employers who are hungry for skilled employees due to Baby Boomer retirements and the lowest unemployment rate since 1999.
While towns across Minnesota are trying to raise money to fund much-needed technical and trade training programs for high school students, Wright Technical Center already has an 83,000 square-foot school with labs and workshops for more than 70 classes in 12 programs that include health care, welding, automotive technology and law enforcement.
“During the afternoon, evenings, weekends and summers, our building is open and available,” said Brian Koslofsky, Wright Technical Center director. “We’re really trying to establish a greater partnership with industries and make great use of our space.”
Natural Assets
The Technical Center was created in 1971, when many school districts were cutting back on industrial arts classes. By pooling the assets of several school districts, they formed a cooperative that could keep these classes going for students who wanted hands-on learning.
The Technical Center, which also offers some special education and alternative learning programs, trains approximately 650 students every day. It’s one of only six career and tech schools in the state; most of the others are extensions of post-secondary technical or community colleges.
Wright County sits in a gap between the Twin Cities and St. Cloud, a region rich in manufacturing. It’s also growing as the metro area expands geographically, boosting industries such as health care, construction and law enforcement.
“Wright County is projected to be the fastest-growing county in Minnesota during the next 15 years,” said Duane Northagen, executive director of the Wright County Economic Development Partnership. Unfortunately, it’s about 30 minutes to an hour to the nearest technical college. That can be a hardship for adults who have jobs and/or children and can’t wedge another commute into their day.
“The average Central Minnesotan already drives 30 miles each way to work each day,” said Don Hickman, vice president for community and workforce development at the Initiative Foundation.
Offering satellite college classes at Wright Technical Center may make it possible for more adults to get further education or attain certification for better jobs or advancements.
The location also can be convenient for employers who need to train staff but don’t have their own classroom space or available equipment due to around-the-clock manufacturing.
Anoka Technical College has offered certified nursing assistant satellite classes and used the center’s 10-bed hospital unit, and NAPA Auto Parts also has used the Wright Technical Center for employee training, according to Koslofsky. A recent $10,000 Initiative oundation grant to the Wright County Economic Development Partnership will help bring about more opportunities.
“I’m always looking for natural assets that we have in the county to utilize,” Northagen said. “This was one of those big tools that was already in place.”
Tracking Trends
In an effort to meet industry changes and keep up with technology, Wright Technical Center has been upgrading its programs since 1978. More than $400,000 was invested this past summer to add plasma welders to the welding program and a new wheel balancing machine for the auto repair shop.
Northagen plans to use the Initiative Foundation grant to get the word out by connecting with major employers and manufacturing companies, asking them what their biggest needs are and by creating a database of employers.
That may also help high schools do a better job of letting parents and students know about well-paid career opportunities in their own backyards—opportunities that don’t require a four-year college degree and the associated tuition. In some cases, employers may cover a student’s technical college tuition and simultaneously pay them for on-the-job workplace training. “
At a time when virtually every employer is short of a skilled workforce, this is as close to a magic solution as we get,” Hickman said.
WRIGHT TECHNICAL CENTER
Who uses it: Eight member school districts created this alternative high school for kids: Annandale, Big Lake, Buffalo-Hanover-Montrose, Delano, Howard Lake-Waverly-Winsted, Maple Lake, Monticello and St. Michael-Albertville.
Programs: 12 advanced career and technical areas designed for junior and senior high school students include automotive, construction, cosmetology, early childhood elementary education, health science, law enforcement and first responder, welding, graphic communication, introduction and pre-engineering, on-the job training, apprenticeships, and the local Creating Entrepreneurial Opportunities (CEO) program. Students may earn industry certifications and college credits. Wright Technical Center partners with 25 post-secondary institutions, which offer more than 70 different college course options.
For more information:
Wright Technical Center, wtc.k12.mn.us
Wright County Economic Development Partnership, wrightpartnership.org
IN THE PIPELINE
How employers can find skilled workers
Employers in need of skilled workers can also check out Minnesota’s Private Investment, Public Education, Labor and Industry Experience (PIPELINE) program. It offers grants to companies so they can provide dual training that combines classroom work with paid, on-the-job experience in areas of advanced manufacturing, agriculture, health care services and information technology.
About a dozen Central Minnesota employers, mainly in health care and manufacturing, have been among the employers awarded 83 grants totaling close to $3.3 million since PIPELINE was established by the Minnesota Legislature in 2014. More than 670 employees have benefitted from it, according to the Minnesota Office of Higher Education.
The next round of grants will be in the spring 2019. More information is online at dli.mn.gov/pipeline.